Cooling Analysis
- Uniformity of cooling
- Proper cooling line placement
- Evaluate cooling design
- Determine if placement of the bubblers and/or baffle
- Accurate prediction of cycle time
- Optimal coolant temperature
- Recommended design modifications related to cooling
- Isolate potential part warpage
- Reynolds Number
Why Cooling Analysis?
80% of your cycle time involves cooling!
Cooling analysis will accurately simulate any cooling scenario to optimize part quality and reduce cycle times. The cooling analysis can simulate the following, Steel types, cooling, channel size, bubblers,
baffles, coolant temperature, flow rates and Reynolds number can be evaluated for an ideal design and process parameters.
The ability to adjust the cooling simulation allows for
optimized cooling design prior to cutting steel. This can result reduced cycle times and uniform cooling with improved part quality.
Circuiting Analysis
(Coolant Temperature)
Cycle Time Prediction
(Part Average Temperature)
Mold Surface Temperature
Mold Surface Difference
Part Average Temperature
Coolant Temperature
Coolant Flow Rate
Ensuring Turbulent Flow
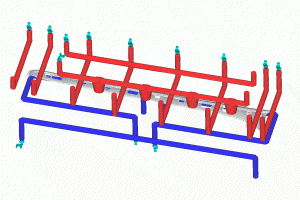
coolant temp
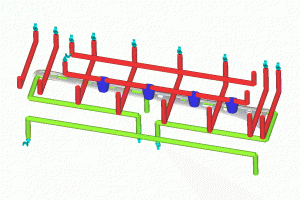
coolant reynolds number
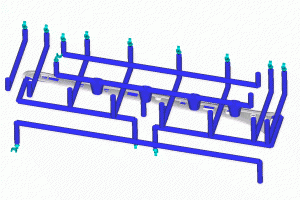
coolant flow rate
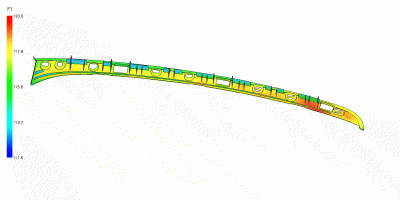
Cool Part Temp core
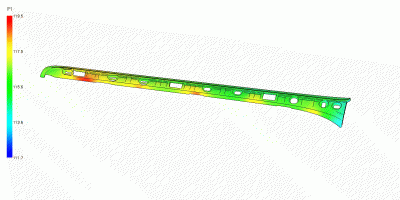
Cool Part Temp Cavity
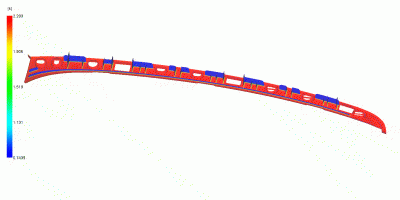
cool part freeze time