Moldex3D Analysis
Moldex3D is the leading innovator of true 3D injection molding simulation software. With the use of Moldex3D’s advanced simulation capabilities MFS can accurately predict temperature, pressure, fiber orientation, viscous heating, and warpage in plastic parts.
The high levels of accuracy that we achieve in our analyses can be attributed to using full 3D mesh for runners, cavities, cooling channels and inserts. 3D mesh, specifically Moldex3D’s proprietary Boundary Layer Mesh (BLM), allows for extra refinement through the thickness in order to capture the unique flow behavior of thermoplastics. Having that extra refinement through the thickness allows us to best simulate the viscous heating that occurs between the laminates of the flowing polymer, which is critical when balancing multi-cavity runners.
Running an analysis with full 3D mesh is the best way to validate final part or runner designs, as it can consider all of the challenging physics that occur in the injection molding process.
Call 877-MOLDFLO today to review options to include a Moldex3D analysis as part of your complete analysis package.
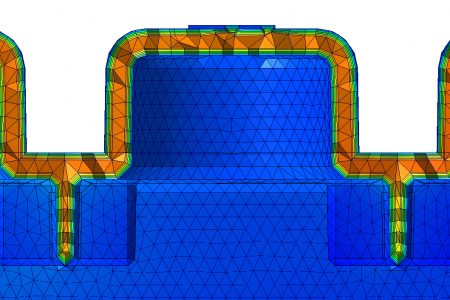
Moldex3D’s Boundary Layer Mesh adds mesh density through the thickness in order to best predict temperature distribution.
- Injection Molding
- Gas Assisted Injection Molding
- Water Assisted Injection Molding
- MuCell (Microcellular) Molding
- MuCell Core Back
- Injection Compression Molding
- Compression Molding
- Co-Injection Molding
- Multi-Shot Molding
- Optics Molding and Analysis
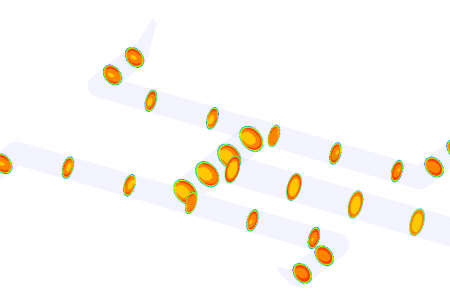
By using Moldex3D, MFS can simulate the viscous heating effect in flowing plastic. The temperature distribution at the runner junctions show how cavity imbalances can occur.